Safran Landing Systems Case Study
Safran Landing Systems (previously known as Messier-Bugatti-Dowty) is the world leader in the design, development, manufacture and support of landing gear systems.
A unique combination of advanced engineering capabilities, integrated systems technology and experience on an exhaustive range of programs enables Safran Landing Systems to provide innovative solutions for a diverse range of aircraft.
Nikken were approached by the company in 2007 to work with them on a project to optimise an Airbus A350 Bogie Beam semi-finish machining application. The ultimate solution required 6 off 583kg Titanium Forgings to be machined simultaneously on a six-spindle Droop & Rein Vertical machine tool platform.
The original application machined 3 bogie beams on a machine where the indexing was carried out manually. Each indexing operation, on this manual basis, took 15 minutes to achieve and required an operator to perform the procedure inside the machine tool – not really ideal in an environment contaminated with Titanium swarf and coolant.
The integration of six components on the machine bed supported by CNC Rotary tables required a degree of engineering ingenuity. With 3,500mm between the centres of the components the solution required Nikken’s TAT320 support tables to be mounted back-to-back on the centre of the machine bed. This optimised space and allowed the distance between components to be kept to an absolute minimum. On the rotary table side six Nikken CNC601B Rotary Tables were mounted at each end of the bed, giving the maximum amount of available space for machining. By achieving this layout additional space is also available on the machine bed to accommodate larger components should aircraft requirements change, increasing the specification size of the component in the future.
With the CNC Rotary tables installed and integrated, each indexing operation takes 15 seconds and removes the requirement for the operator to enter the machine area, which provides a significant improvement to working practices. The ultimate result is a significantly improved run time for a load of six components including ten tool changes, providing an impressive saving in hours. In view of the value of each load of six components it is critical for Safran to ensure the process is optimised to deliver 100% accuracy whilst minimising cycle times.
The CNC control integration was carried out by Siemens, utilizing an 840D Siemens control to drive the six spindle machine tool together with the six CNC Rotary Tables and TAT units.
This is a showcase application for Safran, the efficiency gains achieved by moving to a full CNC solution signal the way forward in the production of large aerospace components, with a continued emphasis on improving processes to minimise human intervention and reduce the time taken to manufacture each component.
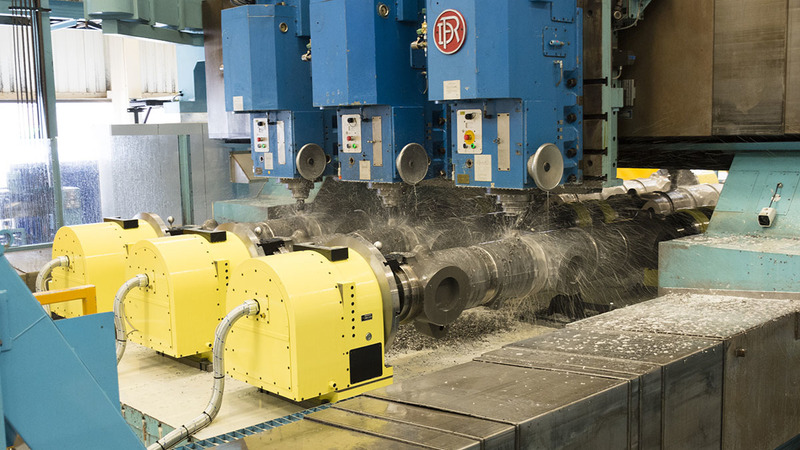
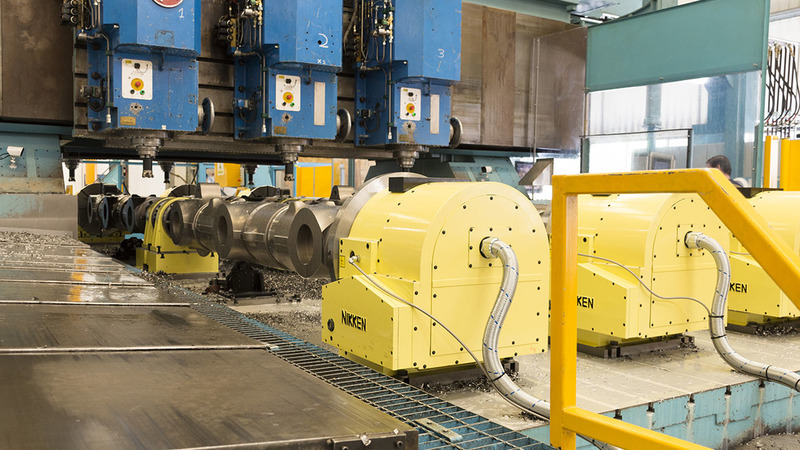
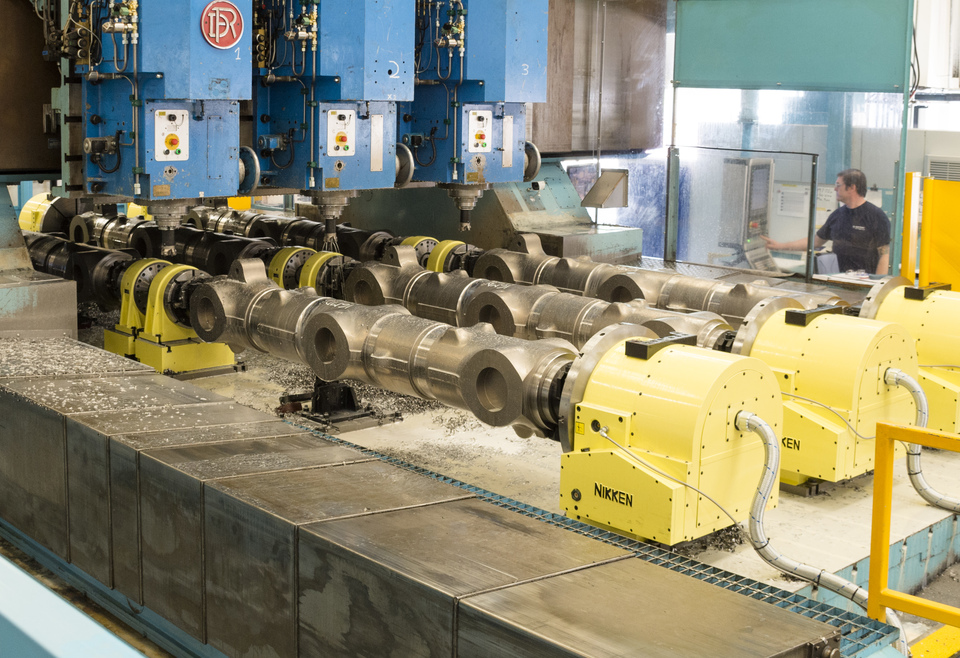