ARMEG Ltd
Market leaders in the design and manufacturing of high-performance power tool drilling accessories, ARMEG are renowned for their incredible quality, extensive knowledge and product innovation. Recognised as part of the prestigious ‘Made in Sheffield’ organization, ARMEG have been serving both the UK and a global client base for over 45 years, providing tool drilling solutions that offer ultimate precision and durability.
Manufacturers of a vast range of complex drilling components, ARMEG regularly undertake intricate machining where accuracy and versatility are key to the manufacturing process.
ARMEG contacted NIKKEN to discuss a replacement rotary solution which they now required within a quick turnaround time. Having previously invested in three NIKKEN Tables for their reputation and incredible precision, ARMEG were confident NIKKEN could provide a high quality set-up with greater capability.
NIKKEN proposed our classic NCT200 Rotary solution integrated with our innovative NIKKEN I/O software, providing incredible precision with the added security of condition monitoring. The compact rotary table to beat, the NCT200 offers an incredible clamping torque of 900Nm and a detachable faceplate, providing the flexibility for work holding solutions in future applications.
With versatility being a significant requirement at ARMEG, NIKKEN also recommended that the solution came equipped with their 'Alpha 21' portable programmable pendant option. This transferable and easy to use controller provides the ability to move and share the full setup between various machining centres as required.
Due to the complex nature of the machining process a few adjustments were required to the proposed angle plate set-up to ensure optimum precision. These were undertaken at the state-of-the-art facilities at the NIKKEN Innovation Centre where a team of highly skilled engineers worked around the clock to complete these custom revisions and deliver the table with a turnaround of just a week.
Since implementation, ARMEG have seen an exceptional productivity increase of 30% which encouraged the decision to increase their capability further, with an investment in a second NCT200 set-up.
Learn more about our NCT200 solution
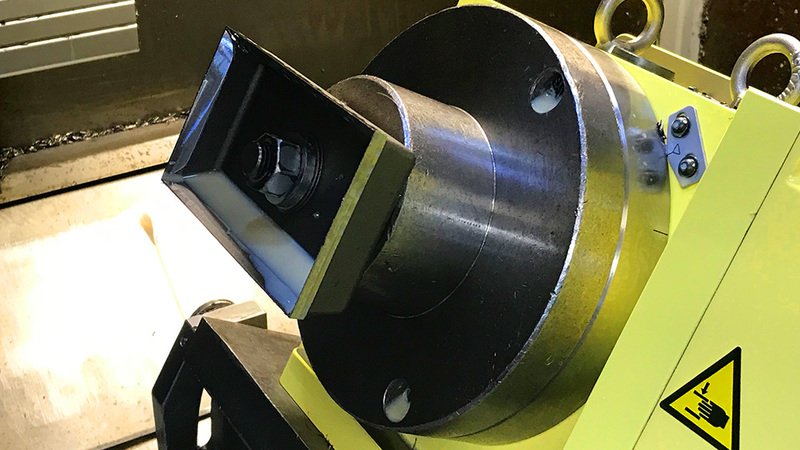
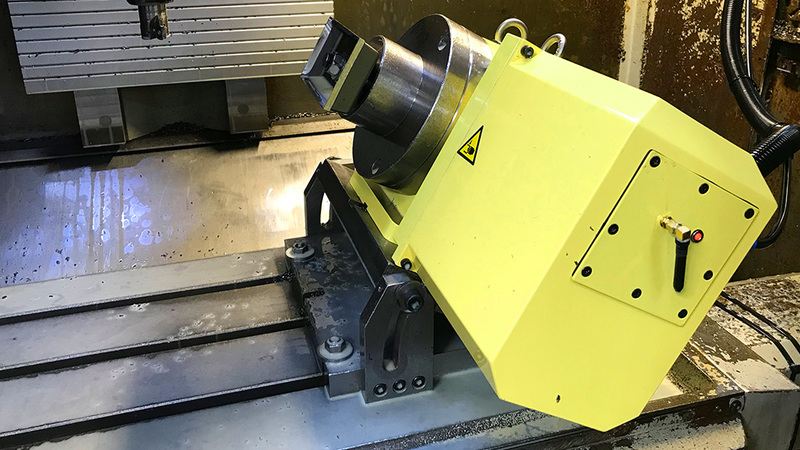