GA Engineering
GA Engineering reduce operations by 66%!
When COVID-19 hit the manufacturing industry, like many others, GA Engineering found themselves looking for ways to make up for lost profit whilst driving the business forward and creating a futureproof workspace allowing them to expand their impressive customer portfolio.
To kickstart plans, GA Engineering began by evaluating the equipment and processes in their workshop consisting of 7 Bridgeport CNC machines, 2 CNC Lathes and various manual machines. With GA Engineering serving a range of industries such as Military, Scientific, Medical, Lighting, Robotic, Communication and Brass furnishing, any machine enhancements needed to be able to provide the adaptability and versatility necessary to accommodate any project sent their way.
Identifying limitations of their standard vices, meaning components had to be manually rotated for additional processing and operations, causing inaccuracies resulting in increased chances of scrap metal, GA Engineering sought to invest in their 3axis machines, converting them into 4th Axis workhorses.
GA Engineering equipped their Bridgeport with their first 4th Axis Rotary Table and work holding set-up, deciding that emulating this on another machine would allow the manufacture of more complex parts whilst reducing scrap material and enhancing machine capacity. The NIKKEN NCT200 Rotary Table allowed GA Engineering to machine the first three operations on lots of their existing jobs in one set-up and negate the need for fixtures to produce angular faces. GA Engineering wanted the opportunity to take on more jobs and improve efficiency, and by installing a second Rotary Table, could provide themselves with flexibility and more scope on the work they can produce. Having already experienced the renowned quality of NIKKEN equipment in previous employment, General Manager, Gary Fullick, approached NIKKEN to build a complete solution to suit their Bridgeport VMC800.
Working with NIKKEN Business Manager Danny Wells, a complete solution consisting of an NCT200 4th Axis Rotary Table, TAT & Trunnion was agreed to provide a cost-effective yet powerful and flexible solution. With a remarkable clamping torque of 900Nm through air supply only, the introduction of the NCT200 alongside the TAT & Trunnion offers the ability to take on a multitude of projects and heavily decrease the number of operations from 6 to just 2.
"From first contact through to installation, communication was excellent, as was service".
Implementing their new solution late last year, GA Engineering have already noticed, through greater accuracy and fewer loads, considerable advantages such as lower cycle times and reduced scrap, which has allowed them to focus their attention on other activities in the business. Now more productive than ever, GA Engineering has begun to work with new customers and projects and expand its portfolio even further.
.jpg)
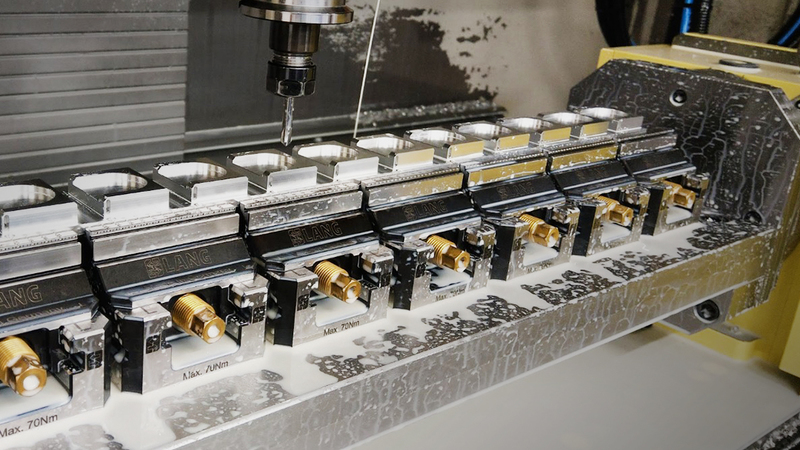.jpg)
For more information on GA Engineering or to find out how they can support your manufacturing needs, visit https://www.gaengineeringgroup.com