High Accuracy Manufacturing with a NIKKEN Slim Chuck
A leading independent UK manufacturer of orthopedic instrumentation contacted NIKKEN for a new solution to aid production for one-off projects through to high volume manufacturing. Given the complex nature of their products, high accuracy manufacturing is key to the company’s objectives.
Previously finding that ER collet chucks did not offer the consistency on run-out accuracy required to achieve the tight tolerances and surface finish, the company chose to investigate alternate tooling methods.
Investing in NIKKEN tooling ensured more efficient and precise machining. Without the heavy time constraints caused by constant machine adjustment production increased, creating a superior manufacturing process with the added benefit of improved tool life.
The example below is a titanium “prosthetic knee cap extractor” which required numerous processes using a NIKKEN Slim Chuck.
The 8-degree taper and positive square shoulder configuration of the Nikken SK collet delivers a higher run-out accuracy over the average ER style collet. NIKKEN’s Slim Chuck with a standard SK collet provides a run-out within 5 microns and by adopting the SK ‘A-Type’ 3 microns is possible (based on 4 x diameter of the cutting tool shank). The NIKKEN solution guarantees the high precision and reliability required for this critical assembly.
Nothing compares to NIKKEN products in terms of accuracy.
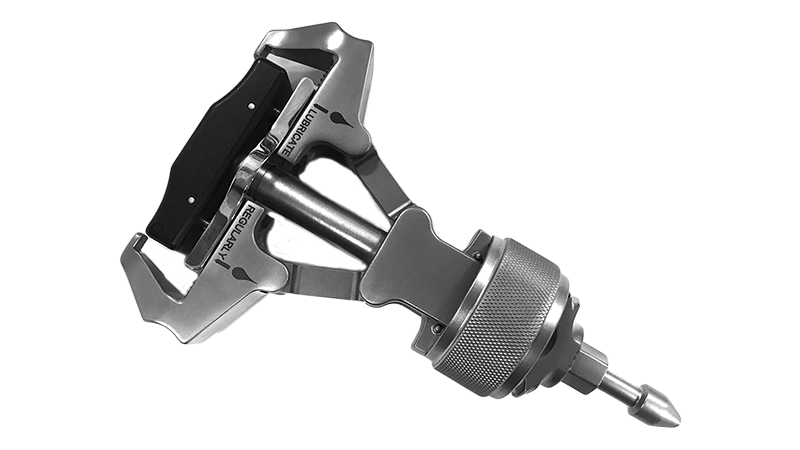
Prosthetic knee cap extractor
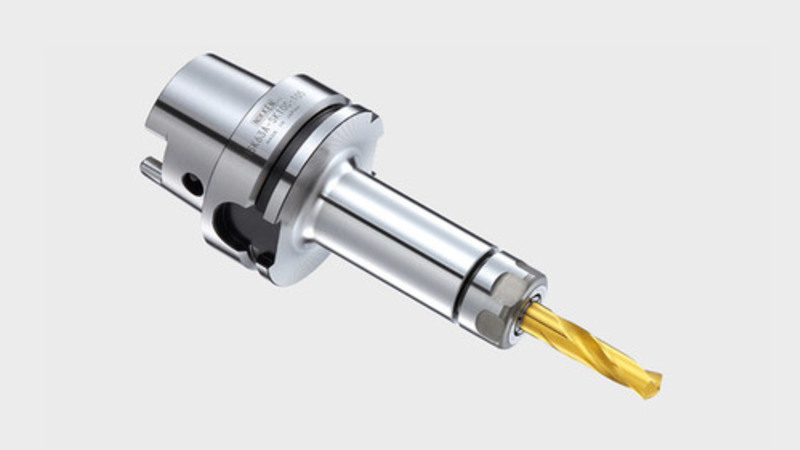
NIKKEN Slim Chuck