X-Cel Superturn Ltd
Providing high-quality solutions to a global client base, X-Cel Superturn Ltd specialises in precision machined components within the petrochemical (including downhole drilling, surface, and subsea applications) power generation, aerospace and construction industries.
X-Cel consulted NIKKEN regarding an up and coming application to machine thirty one 3mm diameter holes at a depth of 44mm inside a component.
This highlighted a requirement for a 90° Angle head solution to provide the approach angle needed to achieve these features, using their Doosan NHM horizontal machining centre, in combination with the additional milling operations necessary for the rest of the part.
Currently, this type of work would require 2 setups on 2 different machines (the horizontal machine for the initial operation with a second operation being fulfilled on a vertical machining centre). The NIKKEN/ALBERTI solution had the potential to enable a single setup on the horizontal machine with the angle head providing a similar machining approach to that of the vertical machine.
NIKKEN recommended their ultimate spindle optimisation solution, offering the BT50-TH90cn-3.5 with NIKKEN SK spindle output. This effectively allows the customer to utilise the benefits of NIKKEN's precision Slim Chuck collet and nut solutions. Not only does this combination drastically improve the accuracy and performance but the angle head is also capable of providing a maximum capability of 100 bar through spindle coolant.
The key benefit to the customer is that, when utilised with the 'J Type' nut system and appropriate 'Jetter' cap, the coolant can be controlled either through or around the cutting tool.
NIKKEN also supplied the tooling solution as an automatic tool changeable head, allowing the operator to auto tool change the head when called upon, saving further setup time on the machine.
In conjunction with the pallet change on the machine and improved cutting environment gained from the Alberti Head, cycle times were impressively improved from just over 1 hour down to 8 minutes, but also saving further by providing additional machining capacity on a VMC!
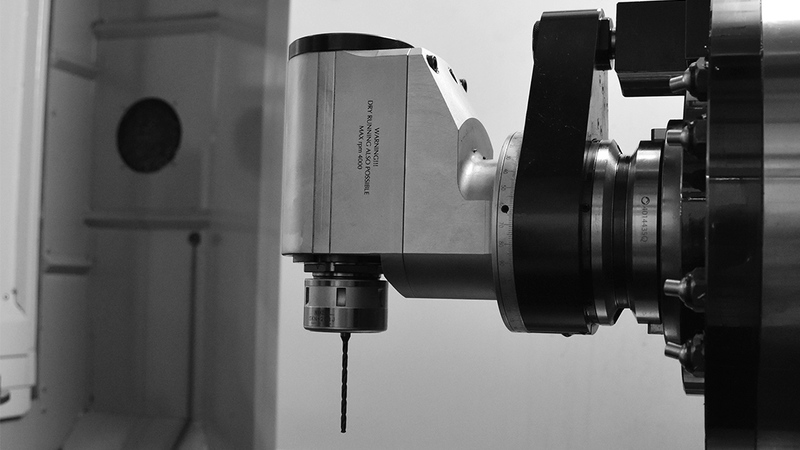
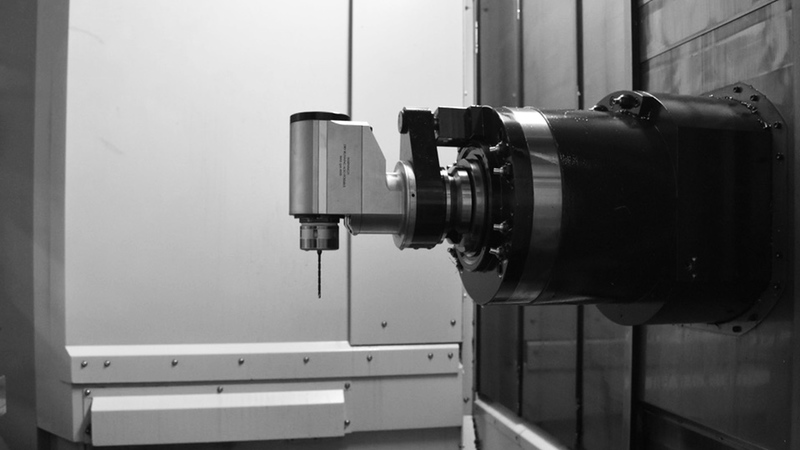