Sink Golf
In 2020, Olly Longlands combined his passion for engineering and golf to create Sink Golf. With a mission to provide a stylish and bespoke range of golf putters, Sink Golf has gone from strength to strength, now manufacturing putters for a diverse audience of amateur golfers, celebrities and professionals worldwide.
Having designed and developed a range of putter models to ensure users would thrive within the sport, Sink Golf acquired a Dugard 3-Axis Milling Machine to begin the manufacture of blade and mallet golf putters.
As a manufacturing starting point, Sink Golf opted for a market average tool holder but soon faced challenges such as endmill movement and low tool reliability, causing exceptional waste and operator intervention.
Seeking a solution to increase tool life, productivity, efficiency and durability, Olly reached out to his local NIKKEN Business Manager, Danny Wells, for support on the application.
We looked at cutter types which were being used and applied the best NIKKEN solution for the specific tool. SINK use various tool paths to manufacture their putters, from Aggressive material removal, which requires a high clamping force to maintain tool life and Profile milling using ball-nose endmills, which require high run-out accuracy and clearance. These applications lent themselves to the NIKKEN multi-lock for material removal and the NIKKEN Slim chuck for profile milling.
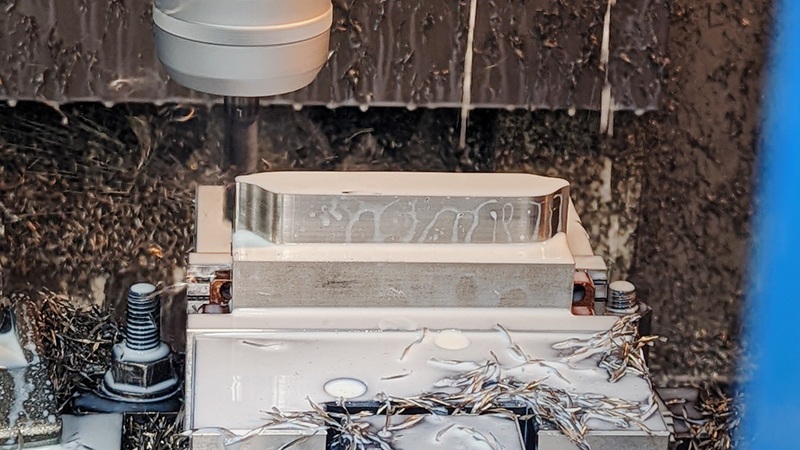
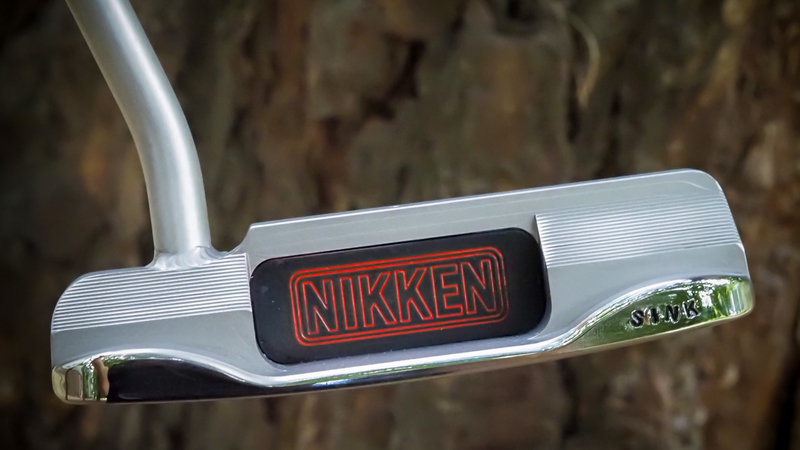
"There was no other reason to pick anyone but NIKKEN solutions when developing my products and processes. Since the introduction of NIKKEN's solution. We've drastically improved tool life, with performance double what was initially achieved. My confidence with the tool holding has increased massively, and I can now confidently walk away from the machine when it's in the cycle to work on the finishing process of my putters. Something I felt I couldn't do when using standard tooling. My relationship with NIKKEN has proved to be a great and an awesome experience."- Olly Longlands
The improvement of tool life has consequently reduced cycle times enabling Sink Golf to push the tools harder on the 303 stainless steel and EN8 materials used in their production process. Ultimately, Sink Golf can now produce more parts within a week, take on more business and increase ROI.
To contact Sink Golf for their high-quality and premium service, visit their website https://www.sinkgolf.co.uk.