Advantages of NIKKEN's Rotary Table Construction
60 years of knowledge and experience in innovation, design, specialist materials, heat treatment and manufacturing technology are built into every single NIKKEN Rotary Table.
Optimised to provide extreme accuracy with ultimate durability, NIKKEN’s world-renowned CNC Rotary Tables go through a unique manufacturing process and construction techniques to ensure critical accuracies and performance can be achieved and relied upon for on any application or process.
DID YOU KNOW?
99% of NIKKEN components are manufactured in house to ensure quality, consistency and longevity of the product.
Faceplate
The unique design of the NIKKEN Rotary Table features the absolute minimum distance between the faceplate and the ION nitrided gear, ensuring high torsional forces can be sustained. NIKKEN tables also feature a limited number of mechanical connections which ensure maximum rigidity. This construction has a proven benefit and allows braking to be applied directly to the main spindle which, fundamentally different to others in the market, is actually a single monobloc component combined with the faceplate.
Unique Worm Screw
NIKKEN use a combination of special hardened steel and custom-made carbide in the manufacture of the worm screw system. Unique in the industry the construction features a hydrostatic high-pressure oil film which greatly reduces the wear between the gears. The precision thread ground carbide worm screw and individually honed, hardened and coated steel worm wheel is then hand-matched and paired together. As a consequence and ultimately benefit the friction between the screw and worm wheel is greatly reduced. This attention to detail allows NIKKEN to maintain maximum thread engagement and rotation accuracy whilst also eliminating backlash and guaranteeing the reliability of the movement.
Casting
NIKKEN utilizes fine grain, high-density grey cast iron castings, ensuring long-term stability, low distortion, high strength and rigidity. These castings are then rough machined and left to stabilize for a minimum of 30 days before being put through the precise final machining and manufacturing processes.
Waterproofing and Protection
To ensure durability, the bearing races of all Nikken Rotary Tables are produced 'in-house' from hardened steel and are fine polished to provide a perfect mirror finish. Located as close to the periphery of the faceplate as possible for optimum rigidity, our radial roller bearings are solid and our thrust bearings are tubular with pre-loading. This can also provide dampening and can protect the internal gears during a crash situation. The edge of the faceplate is also sealed using a unique Teflon face sealing ring to prevent cutting fluid and any ingress from entering the internals of the unit.
LEARN MORE ABOUT NIKKEN ROTARY TABLE CAPABILITIES
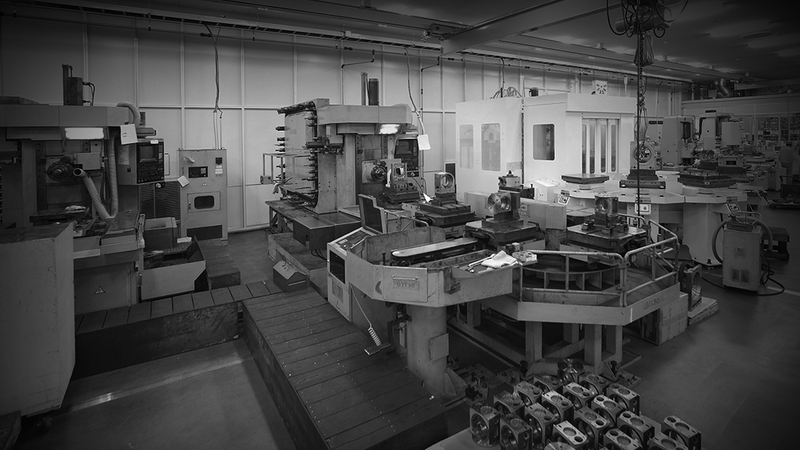
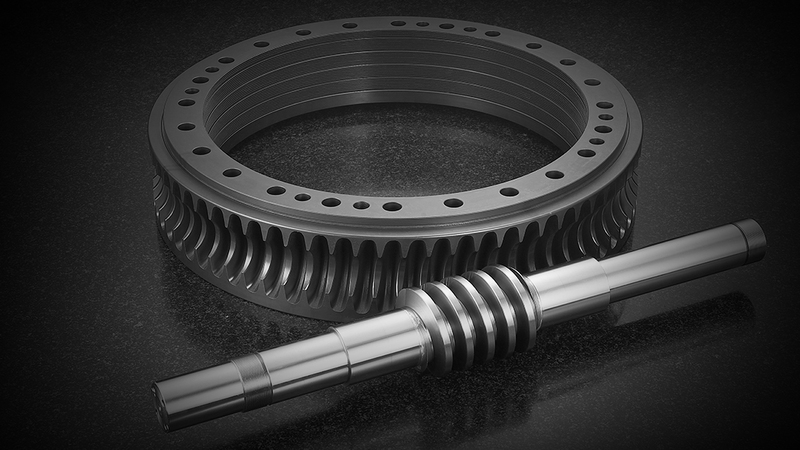