NIKKEN's Involvement in the Motorsport Industry
NIKKEN’s High-Performance Solutions Drive Motorsport Industry Forward as they race away from the competition.
The exacting demands of motorsport, where weight savings, strength, and durability are crucial, require advanced machining solutions. NIKKEN’s CNC rotary tables, NC tool solutions, and precision boring systems are integral to manufacturing engine parts, transmission components, and structural elements that deliver the reliability and performance needed on the track.
NIKKEN’s rotary tables are widely deployed in motorsport manufacturing for their high accuracy and rigidity, allowing engineers to perform multi-axis machining with confidence and precision. Our tables are designed and constructed for extreme accuracy, providing smooth, repeatable positioning that ensures components can consistently meet stringent specifications. This is particularly valuable in creating parts like engine blocks and transmission casings, where every micron matters.
NIKKEN’s tool holders, including amongst others, our world-renowned sub-zero treated Multi-Lock milling chuck and precise Slim Chuck with 8 degree collet system provide exceptional grip and stability, ensuring minimal run-out during machining. This consistency is critical when working with lightweight, high-strength materials such as carbon composites, aluminium and titanium alloys commonly used in motorsport. For engine components subjected to high levels of stress, NIKKEN's tool holders enable the machining of intricate features and fine details without compromising material stability and integrity – a clear demonstration of their rigidity and reliability.
Collaborations with Leading Teams and Manufacturers
NIKKEN’s influence extends beyond simply supplying equipment; it involves collaborating closely with motorsport teams and manufacturers to optimize their manufacturing processes.
Through strategic partnerships, the company provides tailored tooling solutions that help teams address unique engineering challenges. The result is components with enhanced durability, reduced weight, and optimized performance for various racing disciplines.
Formula 1 teams, for example, require parts with extremely tight tolerances. This where products like our Zero-Fit range and comprehensive line of modular boring tools help to provide a means to achieve precise hole making and boring processes. These tools allow for fine adjustments and supremely accurate finishing, essential when machining parts that need to meet exact specifications, such as cylinder heads and crankcases. The vibration-damping properties of these tools also enhance machining stability, resulting in better surface finishes and increased tool life.
In endurance racing, where engines and components must perform reliably over long distances, NIKKEN’s tool holders help ensure accuracy during high-speed machining operations. NIKKEN tool holders minimise tool run-out, which reduces vibration and extends tool life by up five times! This advantage directly translates to improved surface quality on critical components like camshafts and valve components, which must withstand hours of high RPMs without failure.
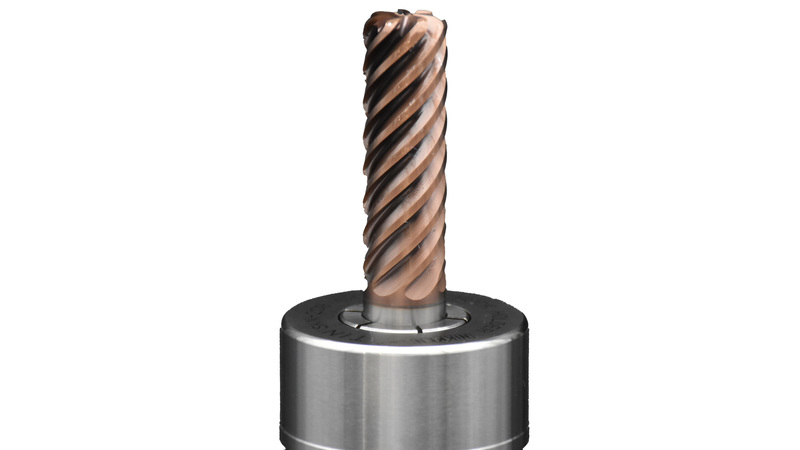
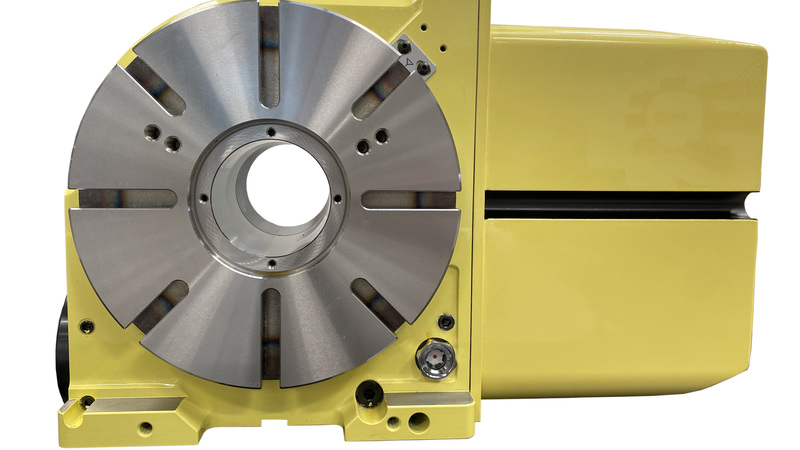
Empowering Innovation with Advanced Machining Techniques
In summary NIKKEN’s single axis and twin axis rotary tables are specifically designed for multi-face machining applications. These products allow for fewer setups, less part manipulation and handling to ultimately provide reduced machine downtime, increased output and higher productivity.
Moreover, NIKKEN’s high-performance tool holders are available, from stock, to suit various machine tool interfaces, including HSK, BT, Polygon, DIN and CAT spindles, making them versatile solutions compatible with an expansive range of CNC platforms. This adaptability is invaluable for motorsport manufacturers who regularly choose and utilise a wide variety of equipment and spindles, to meet their demands, and need absolute consistency across all such cells and facilities.