What impact does runout have on my process and tool life?
FAQ: What impact does runout have on my process and tool life?
Poor run-out at the cutting edge invariably contributes to three key issues which, for productivity and reliability, should be avoided at all costs!
• Reduced tool life and subsequently increased consumable cost! As an example if a typical end mill run-out of 21 microns can be reduced to 3 microns then tool life is increased by approximately FIVE times!
• Run-out contributes to vibration, reduced performance and tool failure! Should a cutting tool have excessive run-out this means that the cutting forces are not equally distributed between the edges/flutes. Effectively all the load is taken up and being applied to only one or two edges which undoubtedly results in increased cutting noise, vibration and premature tool wear/failure!
• The ultimate result of a combination of issues 1 and 2 is the effect on surface finish! The reduction in overall cutting efficiency by applying the loads and forces to a reduced number of cutting edges effectively introduces ‘bouncing’ and deflection during the cut. The consequence of this situation, and not all the edges making equal contact, is unequal chip thicknesses, a variable cutting load/force and consequently a poor and reduced surface finish quality!
All NIKKEN tool holders, as suggested within other FAQ’s, provide as standard better than 5 microns run-out accuracy. By applying your existing cutting tool situation into NIKKEN's New Tooling Calculator we can provide a quick insight into the potential consumable cost savings that could be achieved, based on run-out alone, by introducing NIKKEN's world-renowned Tool Holders to your process.

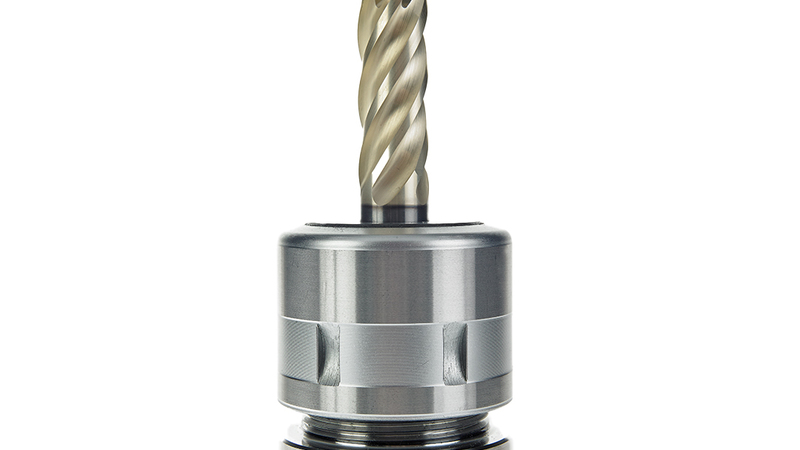