NIKKEN’s standard tool holding solutions, depending on the combination selected, can guarantee and provide run-out at the cutting edge of three microns at four times the diameter of the cutter. This situation and capability provides optimum performance, reliability and tool life for any process or material.
However, if we consider such capability at a tool length outside these parameters or on an older machine spindle, an original accuracy of three microns is scaled and increased proportionally over any extended distance greater than four times diameter (of course the resulting error is considerably greater for less accurate solutions). The consequence of this situation, if not controlled, can be a detrimental decrease in both tool life and performance – a situation no one wants!
NIKKEN developed and introduced ZERO-FIT to counter this problem and allow the physical run-out at any length requirement to be precisely controlled and maintained. This control improves both the life of the tool and indeed the surface finish of the part or component.

-
Two Choices – One Solution
Available in both Multi-Lock (CZF) and Slim Chuck (SZF) configurations.
-
Simple Precise Adjustment
Absolute control of the cutting edge run-out.
-
Balanced Ring with Cam
Available with single or triple Cam design for perfect accuracy.
-
Versatile ‘0’ Fitting of the Accuracy
Either at the tool presetter or directly in the machine spindle.
-
Instant Tool Life Improvement
5 times greater when +20 microns is reduced to 3 microns!
-
Also suitable for NIKKEN Rotary Tables
Flange style options available for faceplate mounting.
The Zero-Fit solution is available across two of our market-leading tool holding solutions. The Multi-Lock Milling Chuck (CZF) and the Slim Chuck 8-degree Collet Chuck (SZF). Both feature a precisely balanced adjustment ring with an internal cam system which provides a physical adjustment of up to 50 microns on diameter. For the Multi-Lock the adjustment ring is mounted directly behind the nose ring which features an increased contact diameter and for the Slim Chuck, the ring is directly in front of the ‘V’ flange. Both systems function in exactly the same way: The initial run-out is measured, the cam ring is rotated to the point of maximum error and then the cam is advanced to reduce the measured value by half.
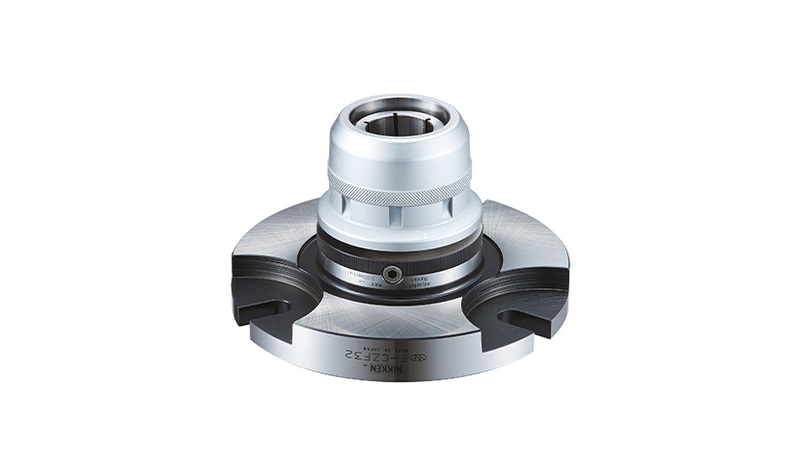
Download the Zero-Fit Holder Catalogue
(PDF - 3.55 MB)
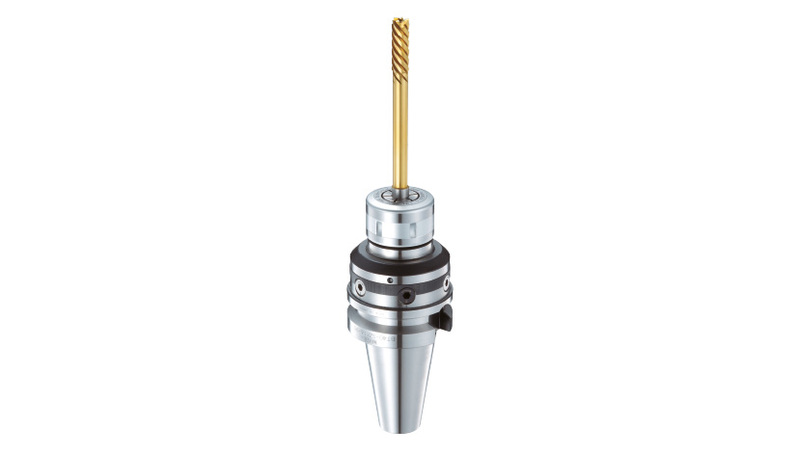
Zero-Fit is available with a single adjustment cam or, as an option, with a 3-point cam system. The 3-point solution provides a central ‘master cam’ for initial adjustment and then two additional cams to the left and right of the master for further fine adjustment of the accuracy (the 3-point option is not available for all Zero-Fit holders – please check for more information).
A recent innovation and addition to the Zero-Fit range is our Zero-Zero solution. Specifically designed for turning machines and CNC lathes which utilise turrets Zero-Zero takes adjustment and elimination of error even further.
The holder not only provides radial adjustment of the run-out, in the same way as Zero-Fit but also features a unique axial adjustment system to allow any misalignment between the centre line of the turret and that of the spindle axis to also be fine-tuned!
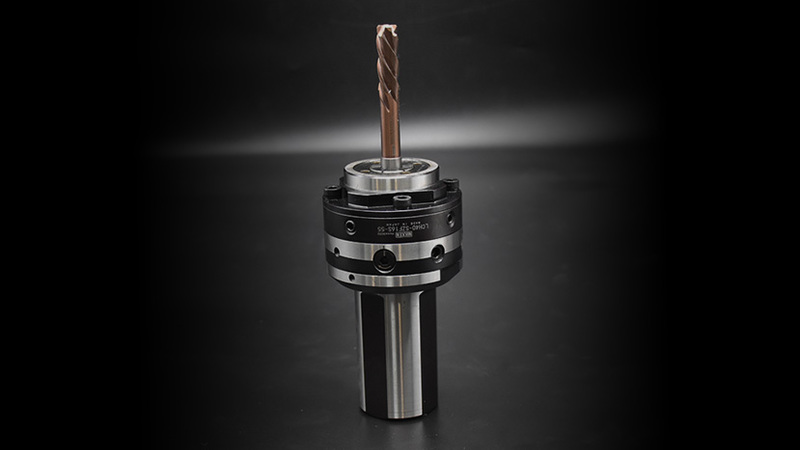