Q. What is the advantage of using a trunnion setup on a NIKKEN CNC Rotary Table?
A trunnion setup enables multiple loading of components and enables you to machine multiple sides/facets in one operation.
The following example shows how you can load 8 basic prismatic components onto a trunnion fixture and produce 4 finished parts every completed cycle providing reduced fixturing, setup times and also equating to longer machine cycle utilisation time. In turn, this allows the operator to do complete other duties/run other machines.
The trunnion setups can incorporate the Zero Point system allowing reduced component loading in the machine time but enabling a quick and accurate fixture change over at the end of the cycle. This enables the reloading of the fixture to be completed while the machine is running the next set of components.
The quantity of components depends on the physical size, but it is possible to load multiple quantities with the correct fixturing.
The number of cutter changes is also reduced, which in turn reduces the process machine time and in turn, reduces cycle time per part and so cost per part.
With labour calculating at approximately 45% of the total manufacturing costs, this is the most significant and easiest target to create cost savings in the manufacturing process. By freeing up the operator to run more than one machine effectively, we are reducing the labour burden on the manufacturing costs of each component.
- Maximise capacity and productivity
- Balance out cycle time in multi-machine volume production (takt time)
- Allows the buffering of short cycles into one longer cycle
- Operator flexibility.
- Labour cost reduction.
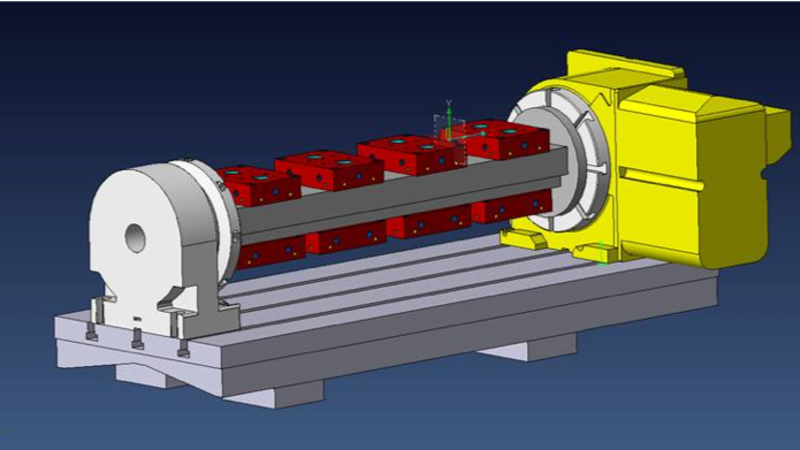