Q. Why 5 axis and not 4 axis?
A. Where 5 axis comes into its own is in the production of complex prismatic/multi-feature components. This is when the features require to be manufactured to a tight tolerance on multiple faces and using a 5 axis rotary table you can machine these features with one setup using the same datum.
This example shows the 5 axis rotary table being used for the first operation using a Triag direct stamping centring vice. This enables the raw material size for the component to be reduced due to only requiring 3mm for the work holding. Operation number two is set on the opposite end of the machine bed utilizing the machine beds capacity but also giving the ability of both 3 axis and 5 axis operations on the same machine.
This also enables all features to be inspected on the first operation and reduces the chance of multiple scrap or rework components from the initial set up by the operator.
- Single operation process
- Complex features
- Difficult to hold components
- Compound / Angular features
The superior quality of build in the Nikken Rotary tables give the confidence that when the cycle start button is pressed, the next component will be correct and to the process requirements. The net result is lower rework or scrap contributing to lower cost per part. By utilizing the whole machine bed productivity and output is fundamentally increased with a longer cycle time - freeing the operator to undertake other duties or multiple processes.
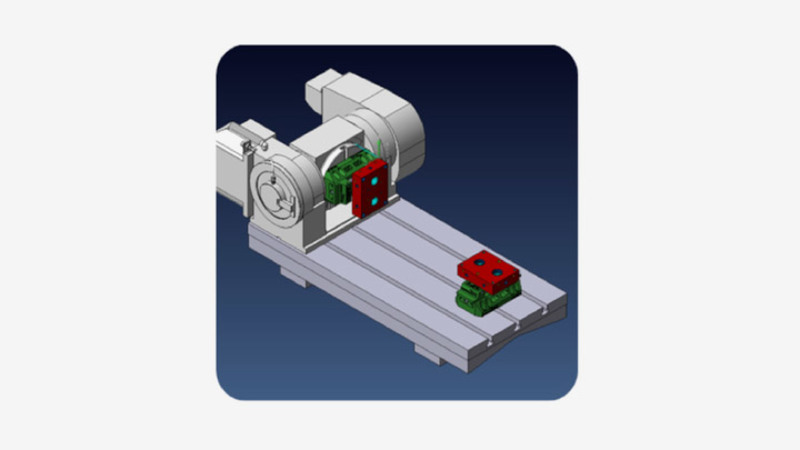